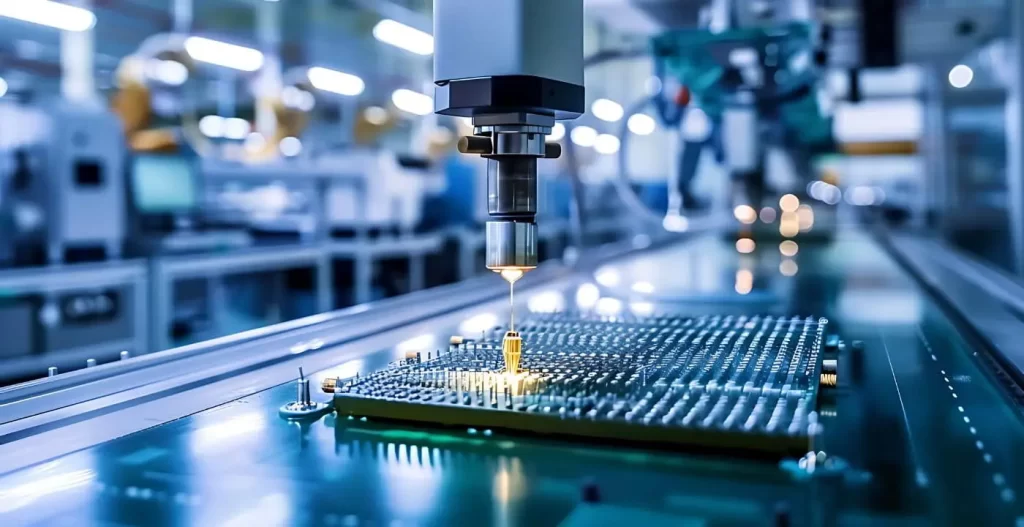
As semiconductor manufacturing becomes increasingly complex, the demand for higher precision, efficiency and scalability has driven the adoption of automated metrology systems. Traditional manual inspection methods are no longer sufficient to meet the stringent quality requirements of advanced chip fabrication. Erik Hosler, an expert in semiconductor process optimization, underscores how automation is transforming metrology by increasing productivity, improving consistency and minimizing human error in semiconductor manufacturing.
The Need for Automation in Semiconductor Metrology
With semiconductor nodes shrinking to the sub-5nm range, the industry faces challenges in maintaining accuracy, throughput and repeatability. Manual and semi-automated inspection processes often introduce variability, leading to inconsistencies in measurement results. Automated metrology systems address these challenges by providing real-time, high-speed and high-precision measurements that optimize process control and defect detection.
Automated metrology plays a crucial role in:
Wafer inspection: Ensuring that nanoscale defects are detected early to prevent yield loss.
Process control: Adjust fabrication parameters in real-time based on metrology feedback.
Equipment calibration: Maintaining measurement consistency across multiple production lines.
By integrating automation, semiconductor fabs can scale operations more efficiently, meeting the growing demand for high-performance, energy-efficient devices while reducing production costs.
AI-Driven Metrology: A New Standard for Accuracy
The combination of artificial intelligence (AI) and automated metrology is redefining semiconductor manufacturing. AI-driven tools analyze massive datasets from wafer inspections, identifying patterns and optimizing measurement parameters in ways that traditional methods cannot.
“Leveraging artificial intelligence in both transistor design, device layout and the overall manufacturing and process control technology will reshape semiconductor manufacturing,” mentions Erik Hosler. By applying AI-driven analysis, fabs can minimize measurement errors, enhance defect detection and accelerate production cycles, all while maintaining the sub-nanometer precision required for next-generation chips.
Predictive Maintenance: Preventing Downtime and Improving Yield
Beyond accuracy, automated metrology contributes to predictive maintenance, ensuring that critical inspection tools remain operational. AI-powered systems monitor real-time equipment performance, detecting early signs of degradation before failures occur. This proactive approach minimizes unscheduled downtime, preventing costly production delays and improving overall yield.
For example, in extreme ultraviolet (EUV) lithography, metrology tools must maintain optimal calibration to prevent exposure defects. Automated systems continuously adjust focus, alignment and overlay measurements, ensuring that each wafer meets the required specifications.
The Future of Automated Metrology in Semiconductor Manufacturing
As the industry moves toward 3D-stacked architectures, chiplet integration and AI-driven semiconductor designs, automated metrology systems will become even more critical. The adoption of robotic wafer handling, in-line inspection stations and machine learning-enhanced process control will further streamline manufacturing and ensure higher levels of precision.
By embracing automation, semiconductor fabs can achieve higher scalability, reduced process variability and improved manufacturing efficiency. As chip complexity continues to grow, automated metrology will remain a cornerstone of yield optimization, cost reduction and next-generation semiconductor fabrication.