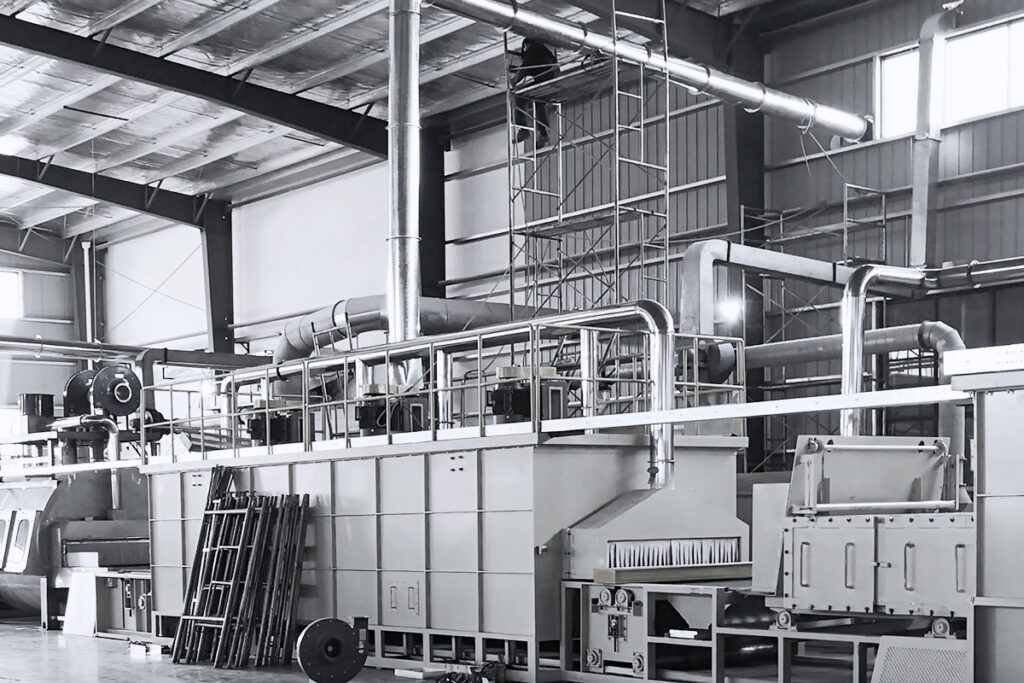
Advancements in Microchannel Heat Exchanger Fabrication for Enhanced Heat Transfer Efficiency
Heat exchangers play an important role in varied industrial processes, including refrigeration, energy technology, and chemical processing. Over the years, researchers and engineers have constantly sought progressive ways to enhance warmth transfer effectivity in these techniques. One area that has seen important advancements is microchannel warmth exchanger fabrication.
The Need for Enhanced Heat Transfer Efficiency
Efficient warmth switch is crucial for maximizing energy utilization, reducing working prices, and bettering total system efficiency. Traditional warmth exchangers, although effective to some extent, often endure from limitations such as large measurement, high stress drops, and suboptimal heat switch rates.
To overcome these drawbacks, researchers turned their attention to microchannel heat exchangers. These devices comprise a series of small channels with hydraulic diameters micro channel heat exchanger typically ranging from tens to hundreds of micrometers. The reduced dimensions of these channels lead to several advantages over conventional heat exchangers.
Advancements in Microchannel Heat Exchanger Fabrication Techniques
Fabricating microchannel heat exchangers requires precise manufacturing strategies. Over the years, a number of developments have been made on this subject, enabling enhanced warmth switch efficiency and improved total efficiency.
- Photolithography and Etching
Photolithography is a broadly used method in microchannel fabrication. It involves using light-sensitive supplies (photoresist) to create patterns on a substrate. By selectively exposing the photoresist to light and making use of etchants, microchannels could be etched into the substrate material.
This method allows for the creation of extremely precise and complicated channel geometries. Additionally, it allows the integration of different features corresponding to fins, which additional enhance warmth transfer efficiency.
- Laser Machining
Laser machining has emerged as another promising technique for microchannel warmth exchanger fabrication. It entails utilizing lasers to take away materials and create microchannels on various substrates.
Compared to conventional strategies, laser machining presents several benefits, including high precision, rapid prototyping capabilities, and the ability to work with a variety of materials.
- Additive Manufacturing
The creation of additive manufacturing, commonly generally recognized as 3D printing, has revolutionized many industries, including heat exchanger fabrication. Additive manufacturing techniques allow the creation of complex geometries with ease.
For microchannel warmth exchangers, additive manufacturing allows for the mixing of intricate inside buildings, such as turbulence promoters, which significantly enhance heat switch efficiency.
Benefits of Enhanced Heat Transfer Efficiency
The advancements in microchannel heat exchanger fabrication strategies have led to several advantages, contributing to enhanced heat switch effectivity:
– Compact Size: Microchannel warmth exchangers offer the next floor area-to-volume ratio, allowing for smaller and more compact designs. – Reduced Pressure Drop: The smaller channel dimensions result in decrease stress drops, lowering the power required for fluid move. – Improved Heat Transfer Rates: Microscale channels promote intensive convective warmth switch, resulting in larger overall warmth transfer charges. – Enhanced Cooling Performance: Microchannel heat exchangers excel in functions requiring environment friendly cooling, similar to electronics cooling or thermal administration in high-power density methods.
Conclusion
Advancements in microchannel warmth exchanger fabrication strategies have opened up new prospects for enhancing heat transfer efficiency. The exact manufacturing strategies, corresponding to photolithography, laser machining, and additive manufacturing, have enabled the creation of microscale channels with intricate geometries and improved performance.
As researchers and engineers proceed to innovate on this field, we will expect further breakthroughs that may unlock even greater heat transfer efficiencies. These developments is not going to solely benefit present industrial processes but additionally pave the way for more energy-efficient technologies sooner or later.